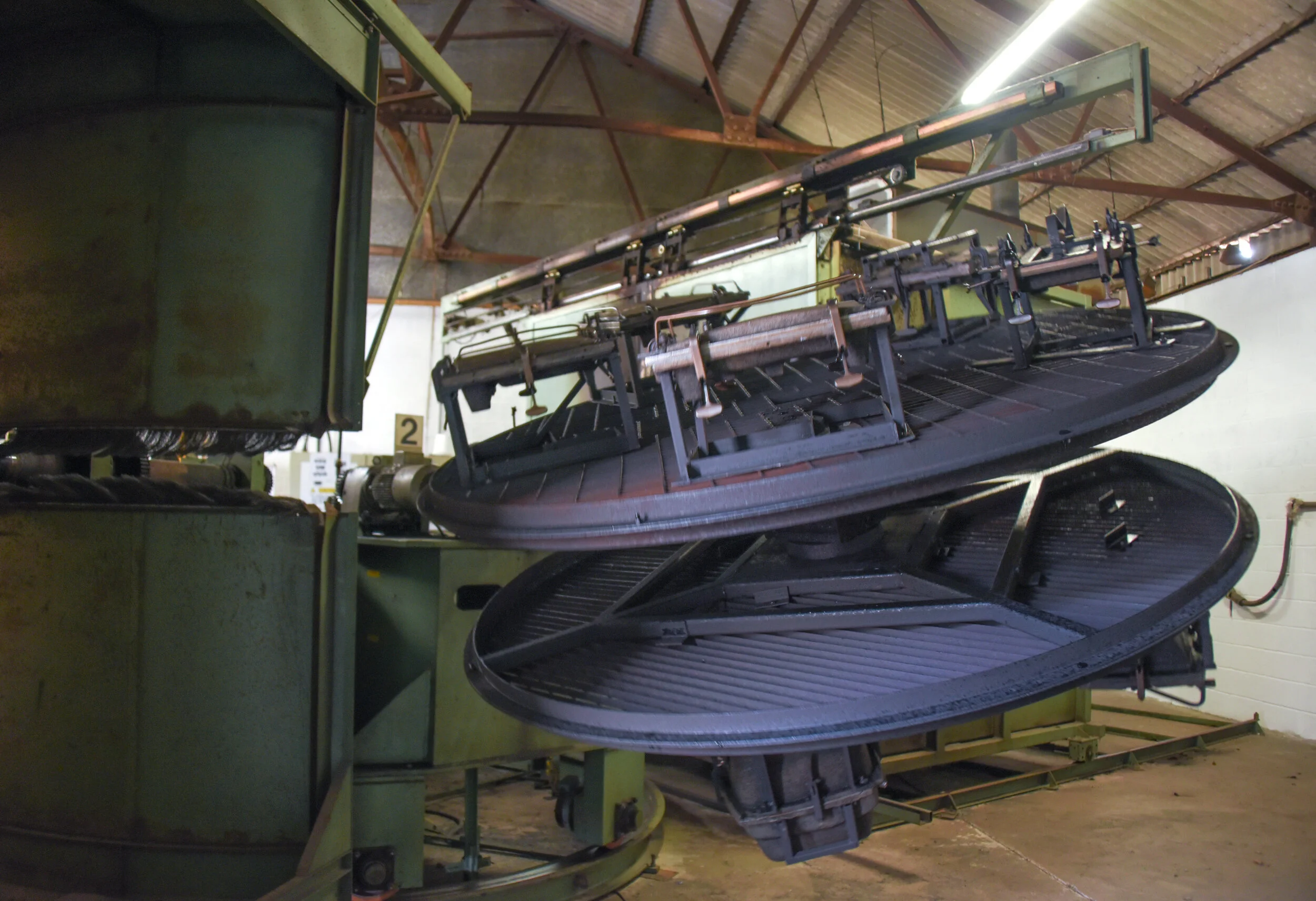
Rotational moulding: the process
How does rotomoulding work?
Four simple stages:
FILL // COOK // COOL // DE-MOULD
As a simple process, you add plastic power to a mould, rotate it at high temperature, cool it down and remove it from the mould. There’s usually some hand finishing too. But to us it’s more than this. We often get involved in the process of refining the design and some of our products are very complex with metal components moulded in.
FILLING
COOKING
The tool is clamped shut and moved into the oven. The oven is heated to between 220°C and 350°C and the tool rotates on two axes at low speed. As the tool heats up the powder melts and sticks to the inner surface of the tool until it has completely melted.
Polyethylene (plastic) powder - which can be coloured to suit your needs - is poured into a tool which is manufactured from sheet steel, cast aluminium or CNC aluminium.
COOLING
The moulded product must be cooled before it can be removed from the tool. There is no residue inside the tool which means no waste material and the tool can be immediately refilled.
DE-MOULDING
The end product is a hollow, virtually seam-free shape with a consistent and even wall thickness.
But wait, we do more!
We have a CNC machine for precision cutting of your product, we can also provide the foam fill for products that require it and will arrange for new tools or collect tools from your existing supplier if you have them. We can assemble to end-product ready for shipping direct to customers and of course you’d expect hand finishing. If you’re looking for rapid prototyping or help with your CAD drawings, give us a shout and we’ll get this sorted for you too.